-
Průběžné zlepšování aerodynamických vlastností kompresorů
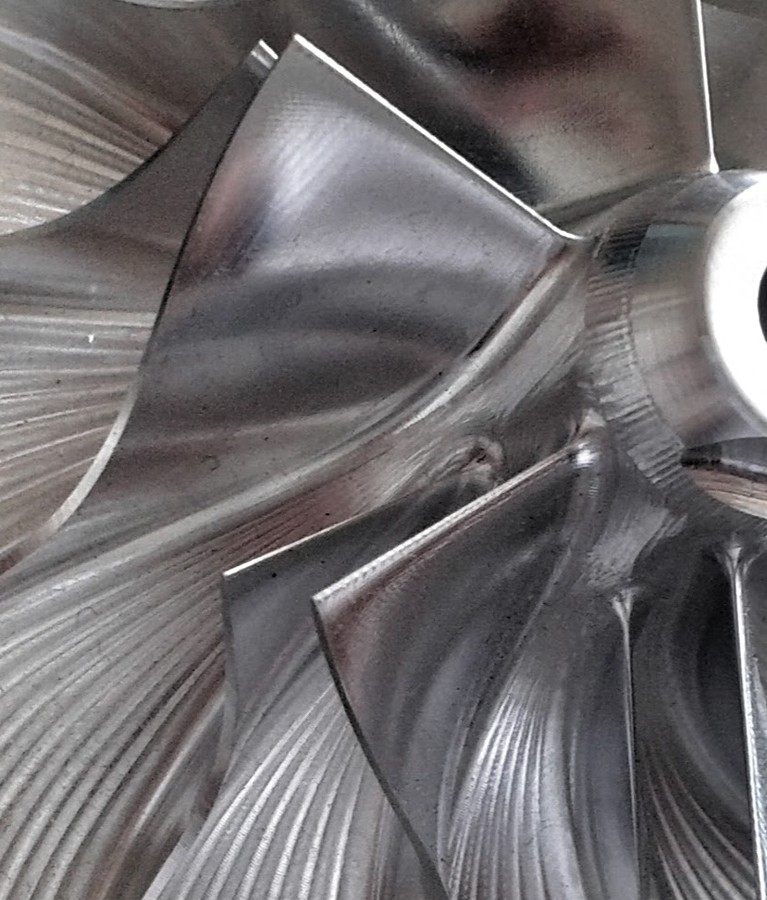
Naši inženýři neustále pracují na zdokonalování aerodynamických vlastností kompresorů a jejich optimálním naladění.
-
Titanové dmychadlové kolo
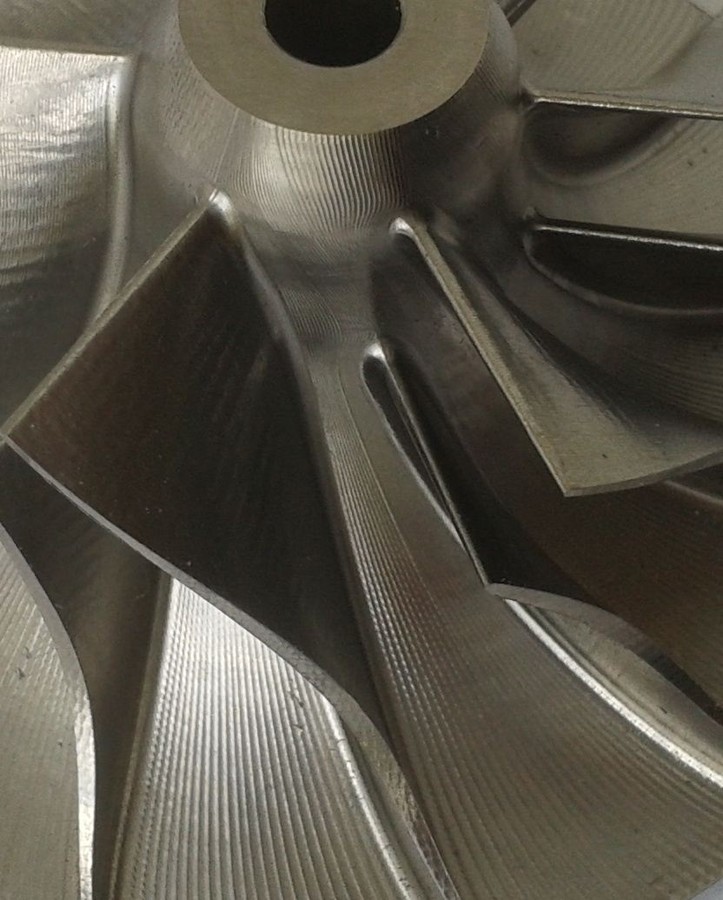
Současný trend výroby komerčních dieslových motorů („downsizing“) zvyšuje mimo jiné požadavky na životnost a pevnost použitých materiálů. Při extrémních cyklických zátěžích některých aplikací je životnost turbodmychadla omezena dmychadlovým kolem z hliníkové slitiny. Řešením je v tomto případě použití dmychadlového kola z titanové slitiny. Obvodová rychlost takového kola dosahuje rychlosti až 600 m/s, vyznačuje se vysokou pevností a bezpečností, dosahuje vyšších stlačení.
-
Od 3D modelu k funkčního prototypu metodou „Rapid Prototyping“
Abychom flexibilně reagovali na rostoucí požadavky našich zákazníků na představení konkrétních řešení ve velmi krátkém čase, začínáme využívat metody „rapid prototyping“, v rámci prototypování dmychadlových a turbínových skříní.
-
LCF
Problematikou cyklické únavy materiálu a únavovými lomy se zabýváme dlouhodobě i ve spolupráci s předními českými vědeckými pracovníky z oboru fraktografie. V roce 2014 jsme vybudovali novou dlouhodobou zkušebnu mimo jiné pro testování, resp. simulaci cyklické zátěže turbodmychadla. Výsledky jsou pak promítnuty do dalšího vývoje a rozvoje výrobního procesu.
-
Lopatkový difuzor
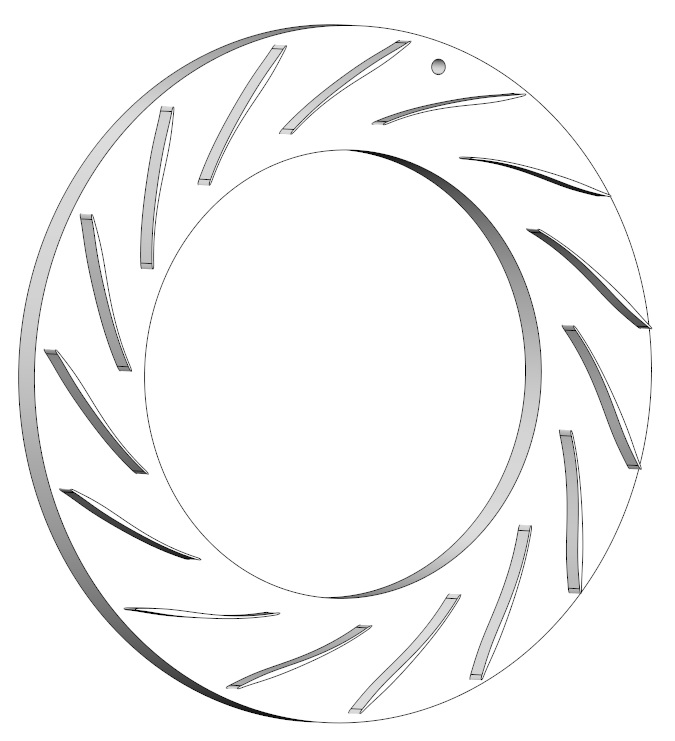
Lopatkový difuzor je set stacionárních lopatek, které obklopují oběžné kolo, jehož principem je zkrácení proudnic v difuzoru, čímž je dosaženo zlepšení účinnosti až o 4%. Je vhodný pro motory s úzkou pracovní charakteristikou (např. generátory).
|